1983年に世界初の「落としても壊れない、丈夫な時計」として発売されてから、G-SHOCKは35年以上にわたって進化を続けてきました。誕生35周年を迎えた2018年には、原点モデル5000系のデザインをフルメタル化したGMW-B5000を発表。いまも品薄状態となっている大ヒット作に次ぐG-SHOCK「36年目の進化」は、なんとカーボンモノコックケースという耐衝撃構造でした。では、なぜカーボンだったのか。その開発経緯などを仕掛け人に聞いてきました!
カーボンでモノコックケースを実現した全く新しいG-SHOCK
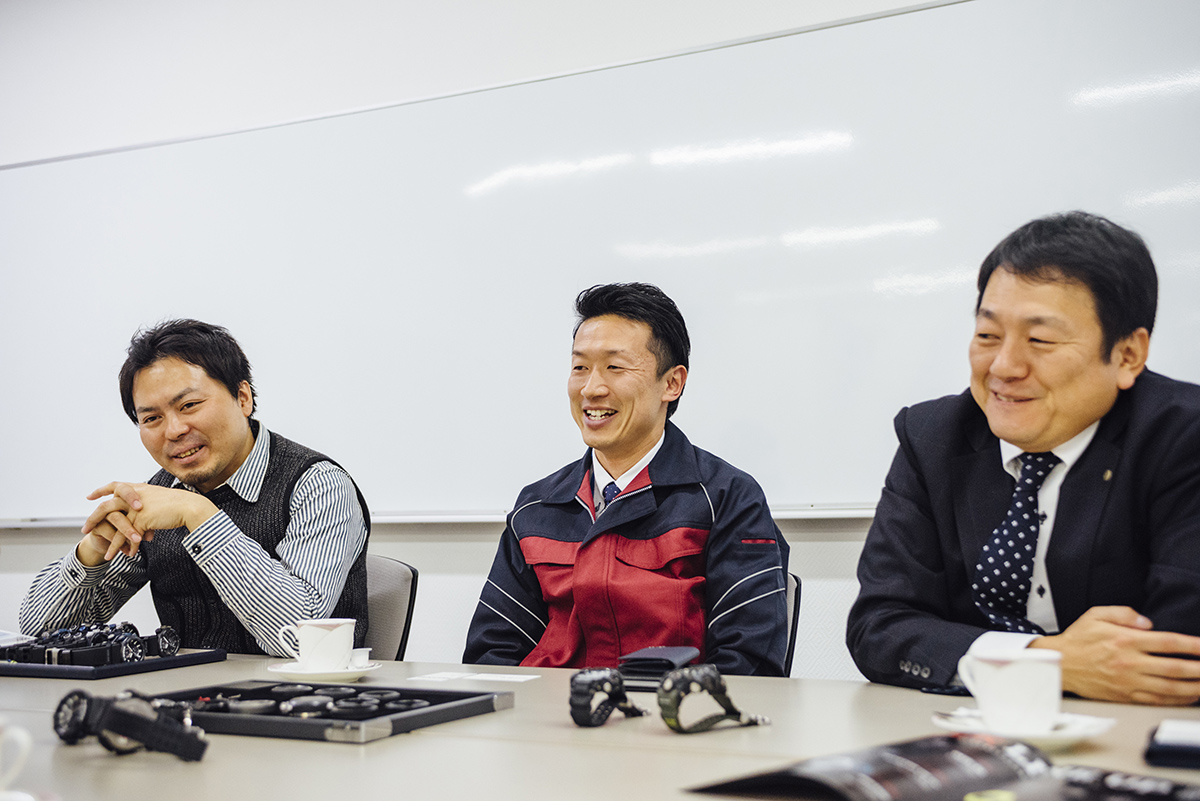
牛山さん:G-SHOCKというのは、常に進化が宿命づけられたブランドです。モジュール、構造、デザイン、そして素材など、広範囲に及ぶ「進化」を考えたとき、私たちが着目したのがカーボンの可能性でした。この素材は、軽量かつ堅牢で、錆びることもない。腕時計にとっては理想的なマテリアルといえるでしょう。一方で、加工が非常に難しいという技術的な問題があります。ただ、これをクリアしてこそ、新しいG-SHOCKができると思ったんです。
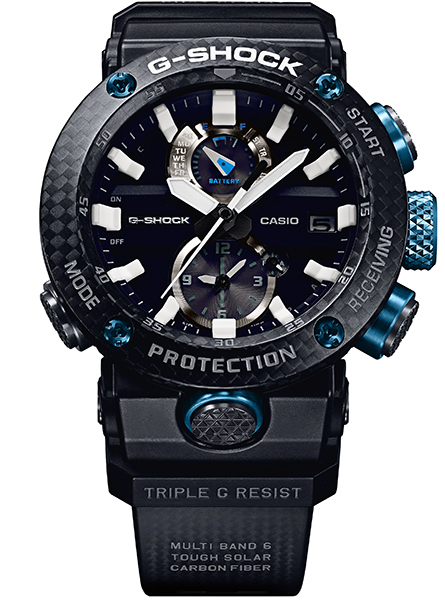
牛山さんは商品開発のマネージャーとして、36年目のG-SHOCKの目玉として新構造を考えていたそう。ただ、自身も理解していた通り、G-SHOCKの進化の方向性を決めるためには並々ならぬ苦労があったようです。
橋本さん:現在のG-SHOCKにはカーボンファイバーをインサートしたバンドを使っていたり、G-STEELの上位機種のベゼルに使ったり、カーボンについての知見は私たちにもあります。ただ、それをケース全体にとなると、やはり初めてのことなのでデザインが決まるまでは悩みましたね。なにしろ新しい耐衝撃構造から考える必要があったわけですから。
牛山さん:このG-SHOCKは、絶対に誰も見たことがない新しいG-SHOCKにしたかったんです。だから、外装はG-SHOCKで初めて裏蓋のないモノコックケースになっています。また、モノコックケースで耐衝撃を実現するために技術者は数十種類の樹脂とカーボンファイバーを組み合わせて最適な配合を評価しました。
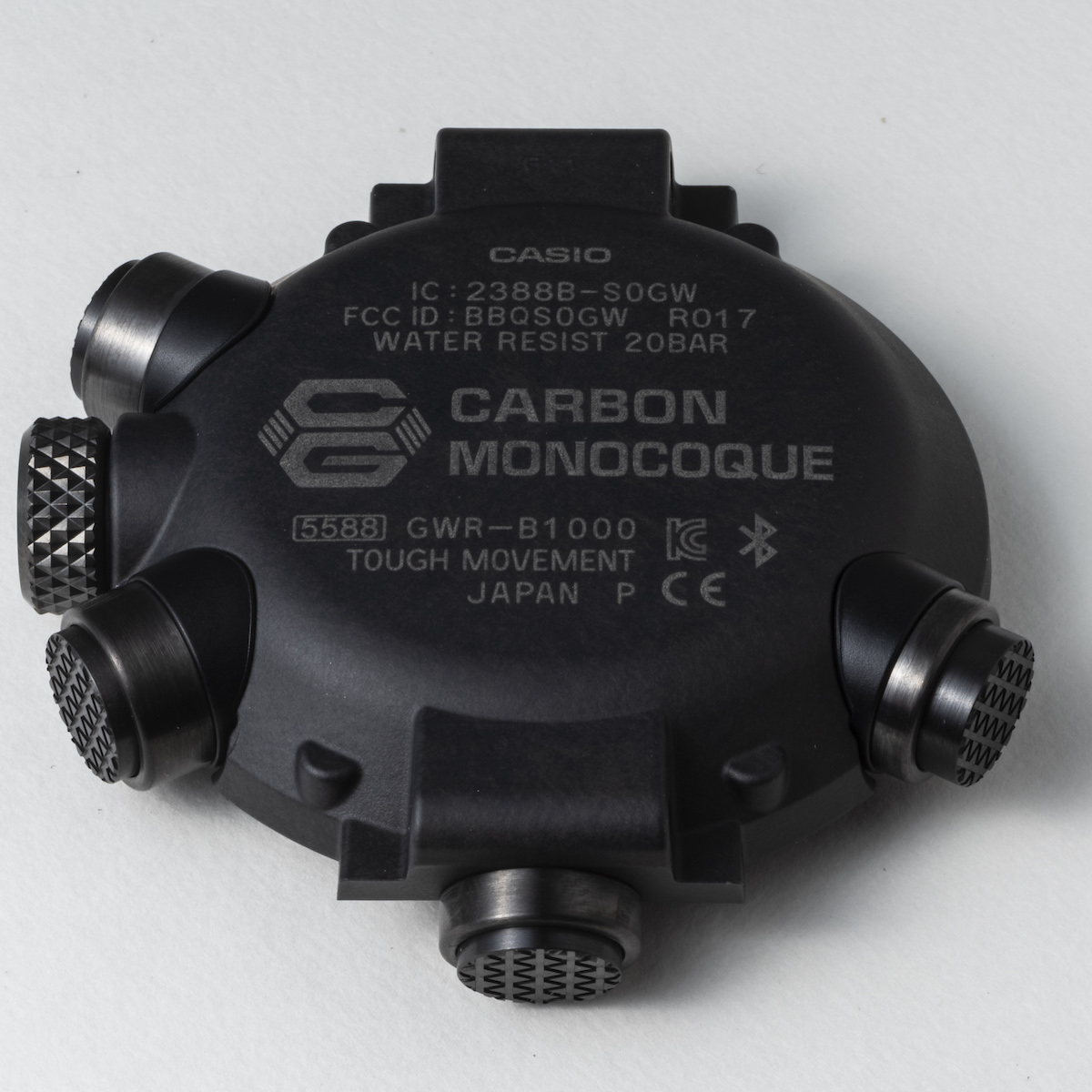
樹脂の成型は、カシオの得意とする技術のひとつではあるものの、新しい素材を使用するには様々な技術課題があります。しかも外装部品であるとなれば、とてもリスクが大きいように思いますが?
櫃本さん:航空業界などで使われるようなカーボンファイバー強化樹脂は、ステンレスの1/4の軽さで10倍の比強度を誇ると言われています。この高機能素材の取り扱いは、かなり試行錯誤しましたね。デザインチームからの出されたモノコックのケースデザインを実現するため、数十種類の材料でケースを試作し、衝撃試験を繰り返すことで最適な材料を選定しました。その一方で、ベゼルは何十層も積層したカーボンファイバーのシートを、熱をかけながらプレスして立体感のある形状にしています。立体形状で瞬間的な衝撃を吸収するのが狙いです。