スクエアG-SHOCKのチタンケースモデルが、11月8日より発売される。一見すると、前年に発表されたステンレススチール製フルメタルスクエアモデルGMW-B5000Dと同じように思えるが、従来機が6万円で展開されているのに対し、最新作は15万円(いずれも税抜)という強気な価格設定。ではなぜ、これほどの高価格帯にしてまでチタンにこだわったのか。その真意を、2名の担当者にインタビューした。
形を変えずに進化を遂げたチタン製G-SHOCK
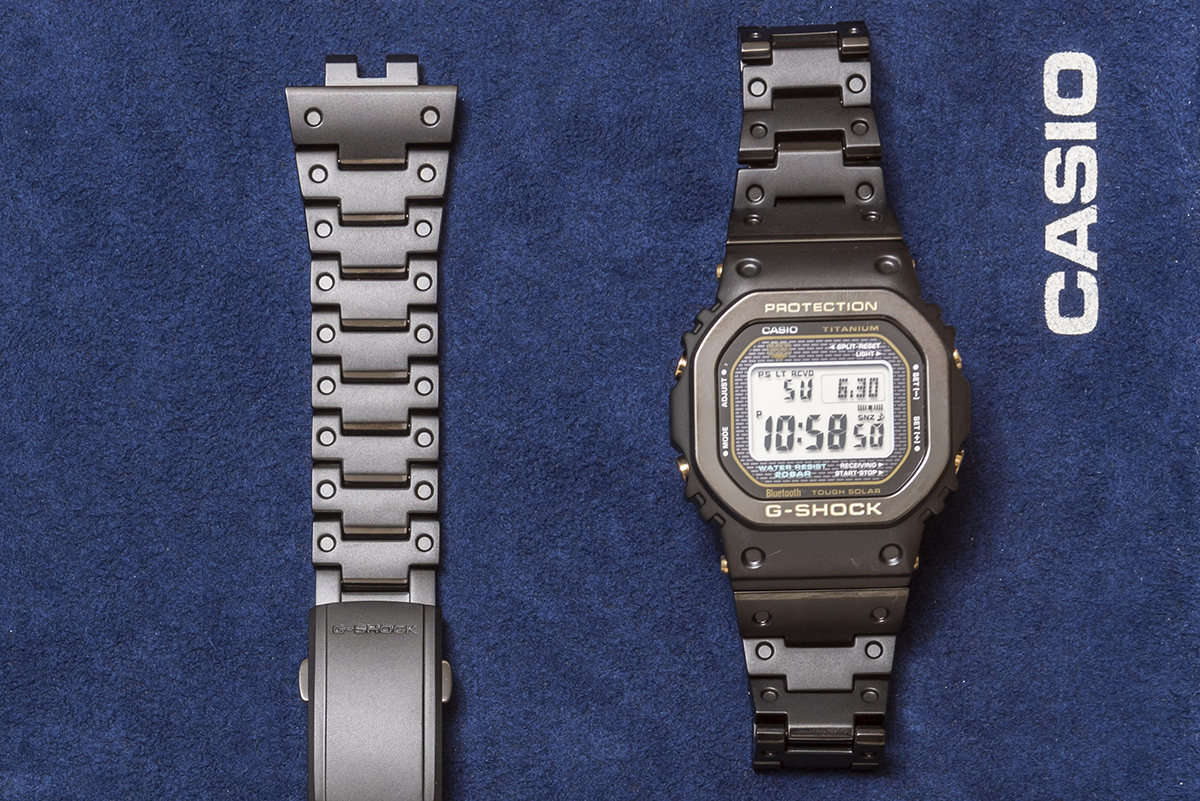
――最も気になるのは、やはり価格です。なぜ、見た目は既存品と変わらないのにこれほど高額になったのでしょうか?
泉さん:確かに形状はステンレススチール製のものと変わりません。というより、このフォルムを変えずに新しいことに挑むことこそが、チタン製スクエアG-SHOCKを開発する原点でした。今年の上半期に展開した第3のマテリアル「カーボン」を使用したシリーズもそうですが、新しい素材へ積極的にチャレンジし続けることはG-SHOCKのアイデンティティでもあるのです。
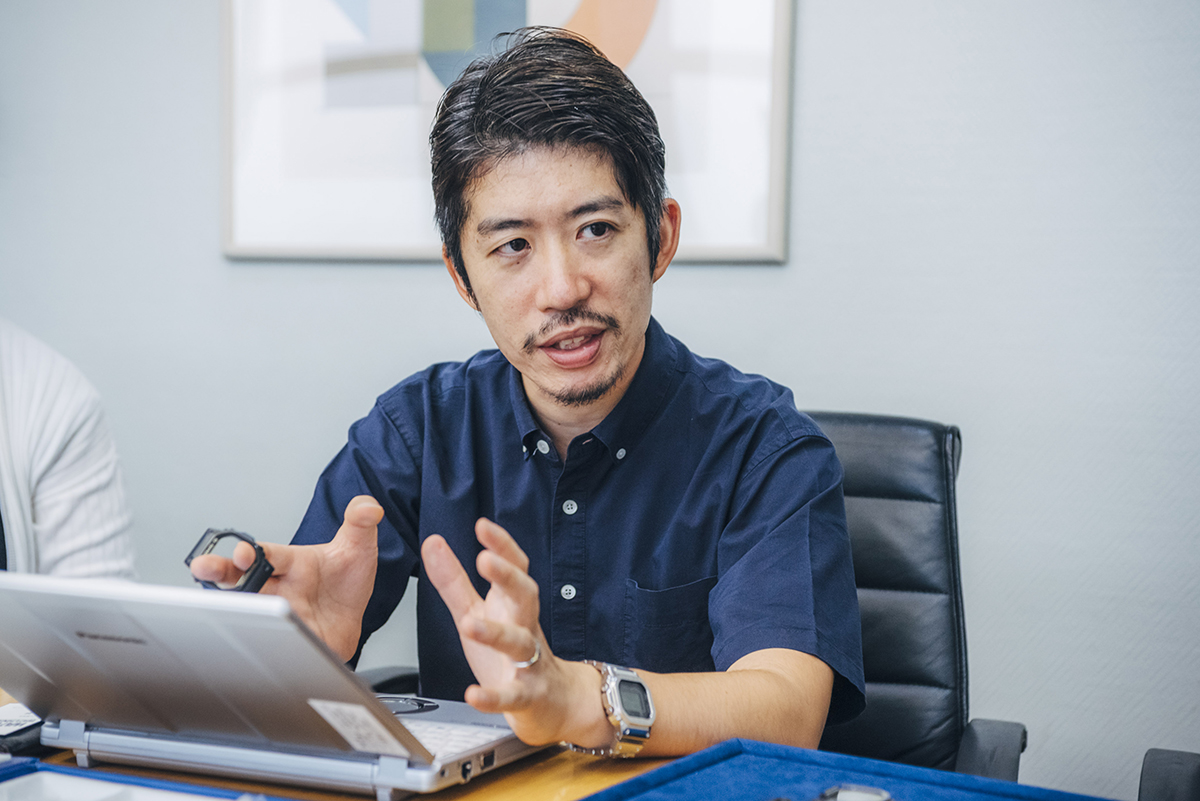
西村さん:ステンレススチールとは素材特性が異なるため、チタンケースを作り上げる専用の金型を新たに導入する必要がありました。外装のデザイン自体は変わらないのに専用の製造ラインを新設したわけですから、このモデルはかなりの高待遇で作られています。
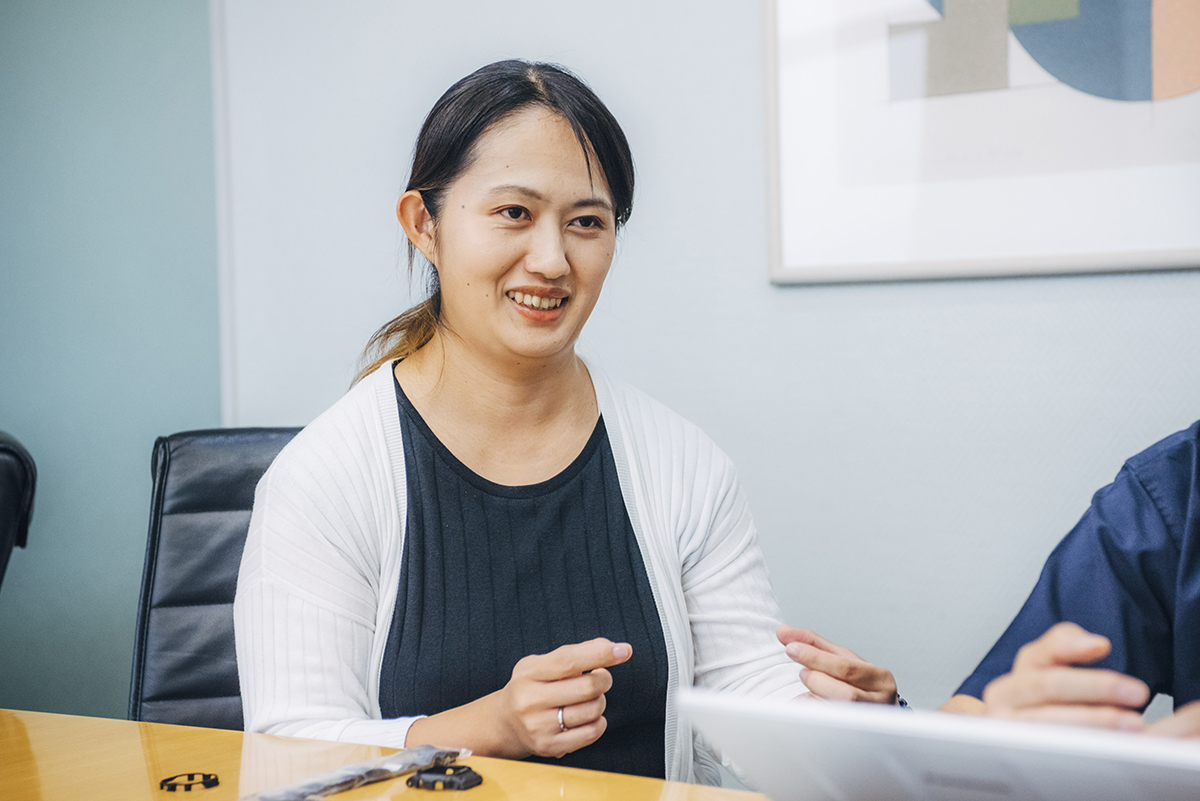
――チタンというと、丈夫な割に軽い反面、キズがつきやすいと言われていますよね?
泉さん:G-SHOCKのプレミアムラインとなるMR-Gのチタンケースの場合、DLC(ダイヤモンドライクカーボンの略)+深層硬化処理という二重の表面硬化処理技術を使っています。対して新作となるチタン仕様ですが、これにもMR-Gに使うのと同じDLCコーティングを表面に施しています。また、ガラスにサファイアクリスタルも使うことでGMW-B5000Dよりも耐傷性を高めるなど、価格に見合うだけのスペックアップをしていると思っています。
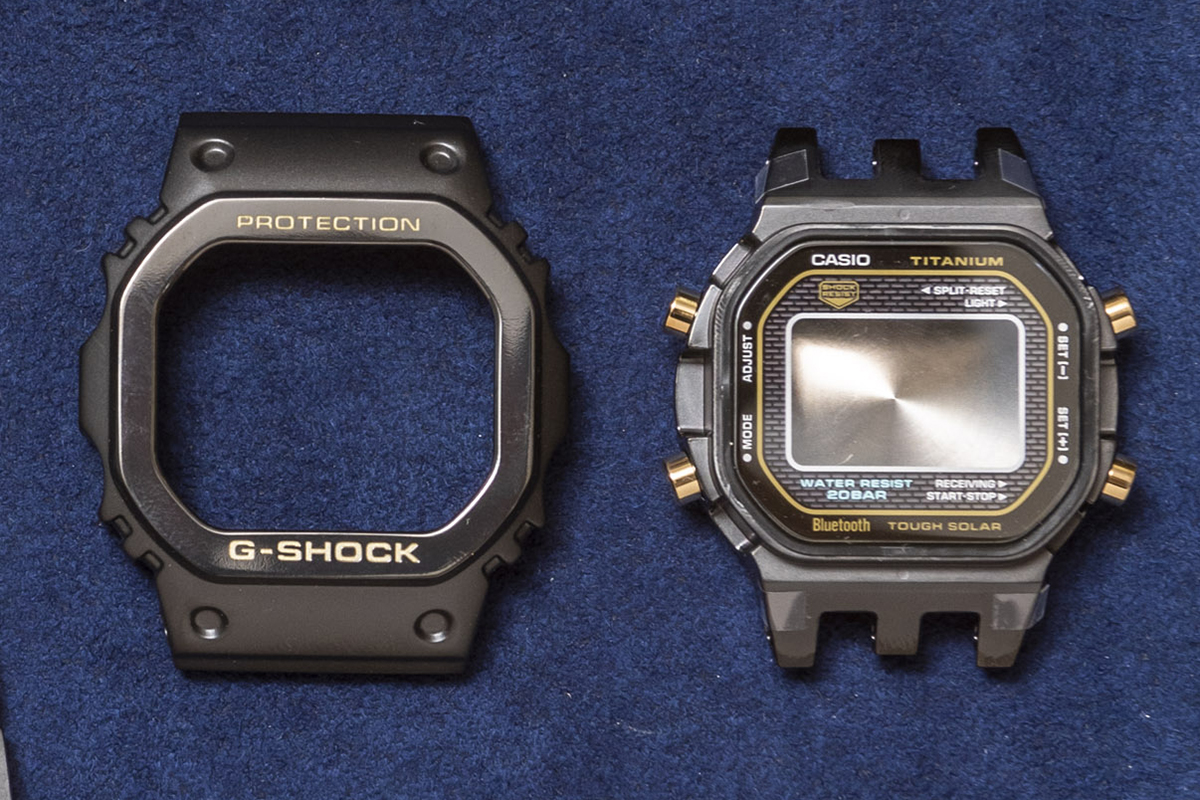
カモフラージュ柄をチタンで表現するという挑戦
泉さん:チタンケースの採用は今後もG-SHOCKが進化するうえで欠かせない過程でしたが、一方で見た目の意外性に欠けるかな、という思いがあったことは素直に認めます(笑)。そこで、チタンケースをベースにして、まったく新しいことにもチャレンジしました。
――9月の展示会で拝見したカモフラージュ柄のチタンモデルですね?
泉さん:このカモフラージュ柄は、顕微鏡レベルで確認できる大・中・小の円の組み合わせで作られています。印刷物における“アミ点”をイメージしていただくとわかりやすいと思います。
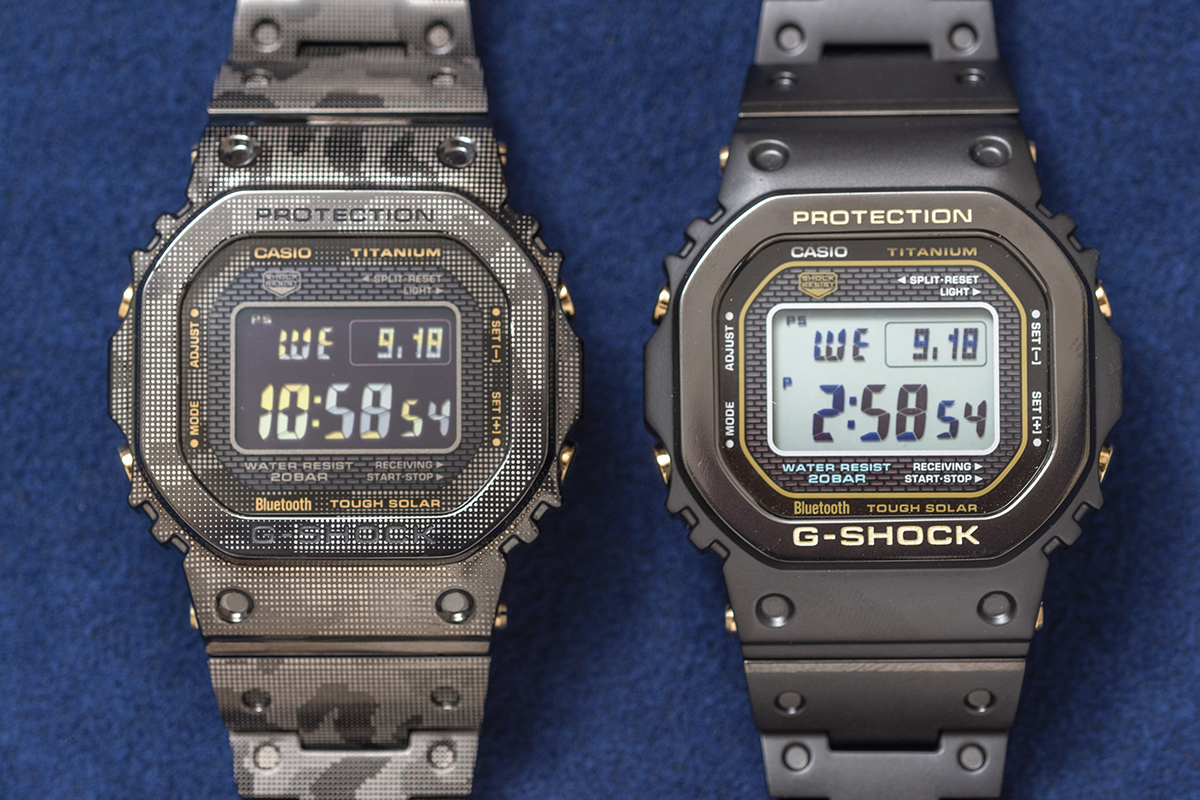
西村さん:この模様は、DLC加工を施したあとに、レーザー加工で表面処理を緻密に削り取ることで成立させています。レーザー加工自体はすでにある技術ですが、これをフルメタルの角型G-SHOCKにどう落とし込むかという点でデザイナーは苦労したようです。ブレスレットをコマ詰めしてもバランスが保たれるよう2つのパターンを組み合わせるなど、細部まで試行錯誤を繰り返していました。こうしてデザイナーが考え抜いたパターンを均一に作る私たちも大変で。パーツにレーザー加工を施すための型にピタリと合わせる必要があるんですが、型に隙間がないとパーツが入らず、かといって隙間があると歪みが出てしまう。結局、歪みなく作るには人の目と手が必要になってくる。なので、ケースも、ブレスレットも、ひとつひとつレーザー加工を行うたびに人の手でセッティングしているんですよ。
アイコニックな“ディンプル”デザインが悩みのタネに
――チタンでスクエアG-SHOCKの耐衝撃性能を保持することは難しくなかったのでしょうか?
泉さん:いまの角型フルメタルG-SHOCKの起源となったフルゴールドのG-SHOCKで培った技術が応用でき、さらに質量も軽くなるので、耐衝撃性能を得ることはさほど難しくなかったです。それよりも仕上げが大変だったとか。実は、2015年にバーゼルワールドで発表したフルゴールドのG-SHOCKを伊部さん(編集部注:1983年の初号機の開発者)とほぼ二人三脚で作り上げたのが彼女なんですけど、あれが出来上がって以降、フルメタルのスクエアG-SHOCKに関わる人たちは事あるごとに西村が作った複雑形状のメタルに悩まされているようで(笑)。
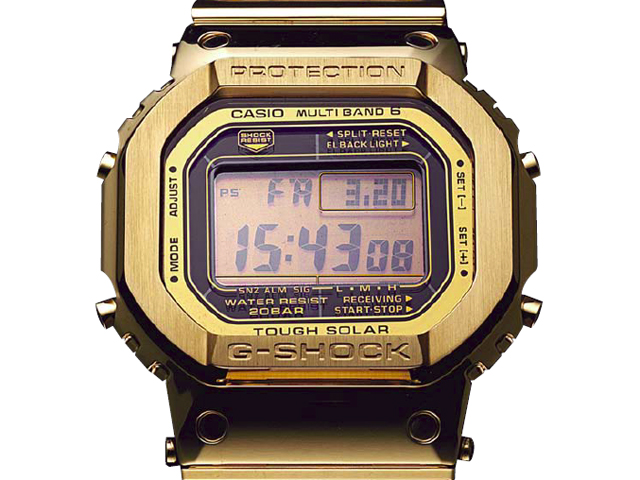
――最高級素材とG-SHOCKが融合した2016年発表のコンセプトウオッチは衝撃的でした。あのモデルのどこかに問題があったのでしょうか?
西村さん:あのときは「1本だけ」という話だったので、ケースとモジュールの間に入れる緩衝材を私が試行錯誤しながらピンセットで貼り付けたりしながら、ハンドメイドの一点物をなんとか完成させました。あのモデルの製作は、誰にもアドバイスを求められない超極秘プロジェクトで、しかも高級素材と対峙しながらピンひとつさえ無くせないプレッシャーも常に感じていたので、ほとんど辛かった記憶しかありません(苦笑)。にも関わらず、私がフルゴールドのスクエアG-SHOCKに取り入れたケースとブレスレットの“ディンプル”(=丸いくぼみ)が、その後の製品のデザインや製造工程でネックになっているんです。そこが議論になるたび、私の辛い記憶も蘇ってくるという……。
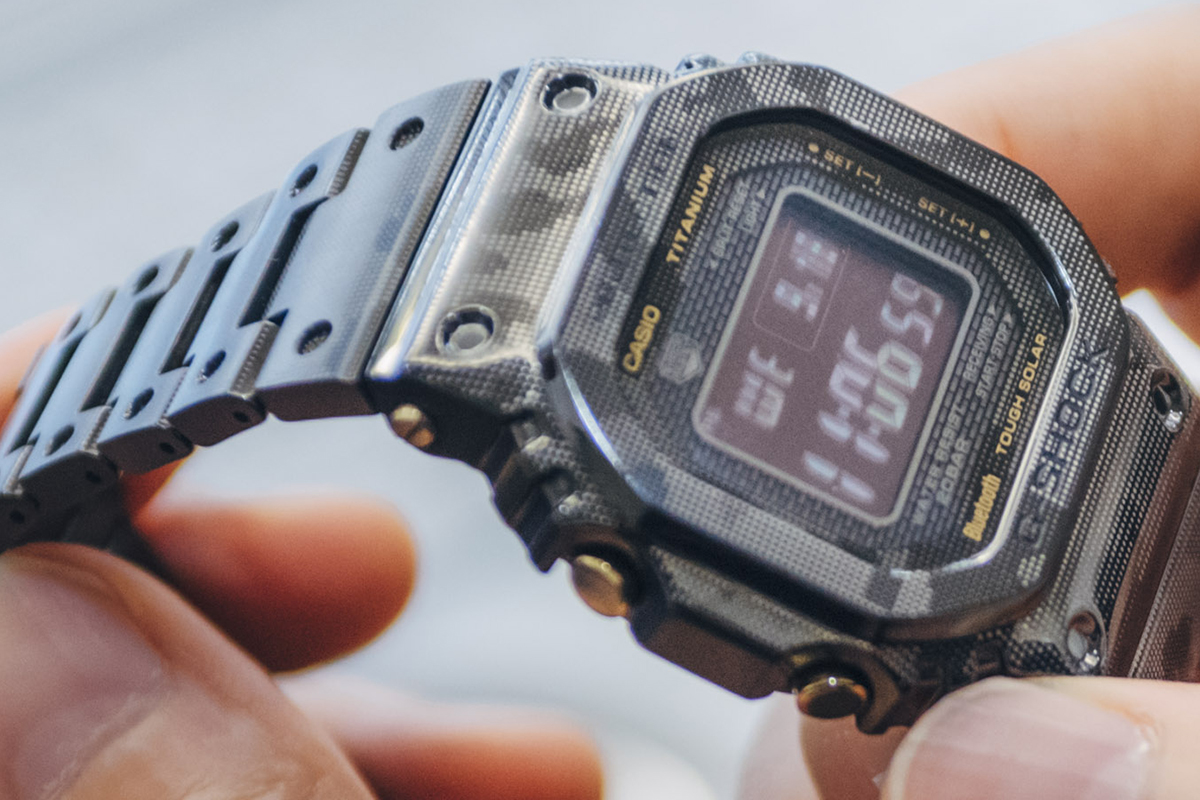
泉さん:彼女は1983年の初号機から続くデザインを“スペシャルな1本”に反映したわけですが、それを金属で作るとなると“くぼみを鏡面にするのか、別の仕上げを施すのか”など、多くの人を迷わすポイントになってしまったんです。
西村さん:「なんでブレスレットのコマにまでくぼみを入れたんだよ〜(泣)」と、周囲からよく言われます。「1本だけ」ということでデザインした当初のこだわりが、いまでは新作を作るたびに大ごとになってしまい……。実はチタンのモデルでも穴の仕上げをどうするか議論になりました。鏡面で磨くのもステンレススチールと勝手が違うので、結果、私も苦労しましたね。
――そんなに苦労を重ねて完成させたのに、期間限定の製造はもったいない気もします。
泉さん:これだけの手間が必要だから、製造期間を限定しないと出せないのです。ただ、せっかくチタンを使うことでステンレススチールと比べて57gも軽量化できたので、その「軽さ」をより多くの方々に実際に手にとっていただきたい。そうすれば、きっとG-SHOCKのアイデンティティである「進化」も感じてもらえることでしょう。
新たな素材を使うことで直面する様々な問題を乗り越え、晴れて完成したチタン製G-SHOCK。確かに高額ではあるものの、その価格の裏付けは十分に取れたと筆者は感じた。加えて、新たなデザインも同時に試すというプラスアルファのチャレンジ精神。こうした、ときにコストや生産性を度返ししてでも「進化」を止めない姿勢があるからこそ、私たちはいつまでもG-SHOCKに惹きつけられるのだろう。
- TAG